The HALT Approach: A Game-Changer In Substance Use Recovery
Discover the HALT approach, a game-changer in substance use recovery. Enhance reliability, reduce costs, and accelerate time-to-market!
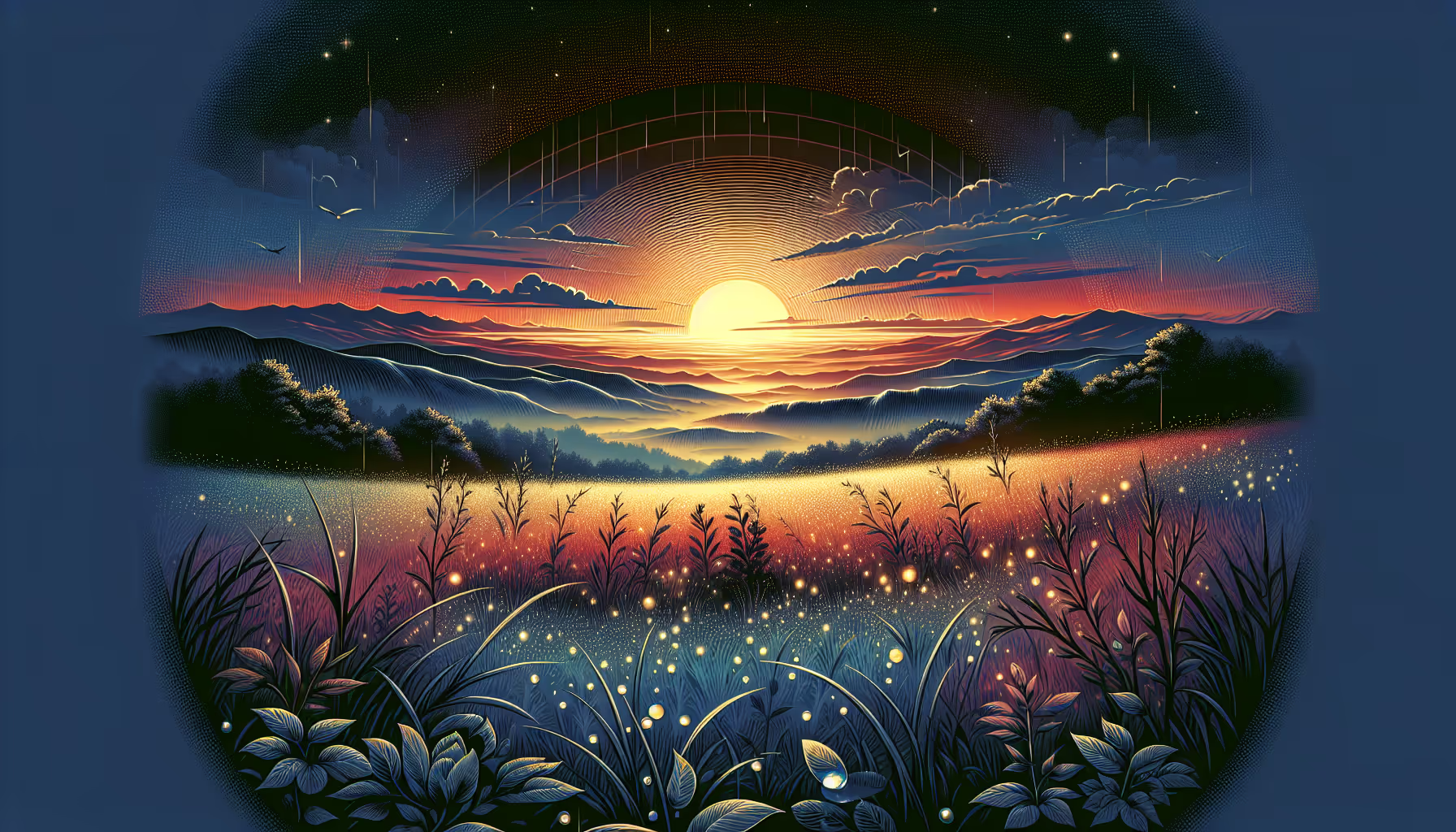
Understanding HALT Testing
To ensure the reliability and robustness of products, manufacturers employ a testing technique known as HALT, which stands for Highly Accelerated Life Testing. HALT testing allows engineers to subject prototypes to extreme stress levels, surpassing those encountered during normal usage, in order to identify design or manufacturing weaknesses [1]. Let's delve into the introduction and importance of HALT testing.
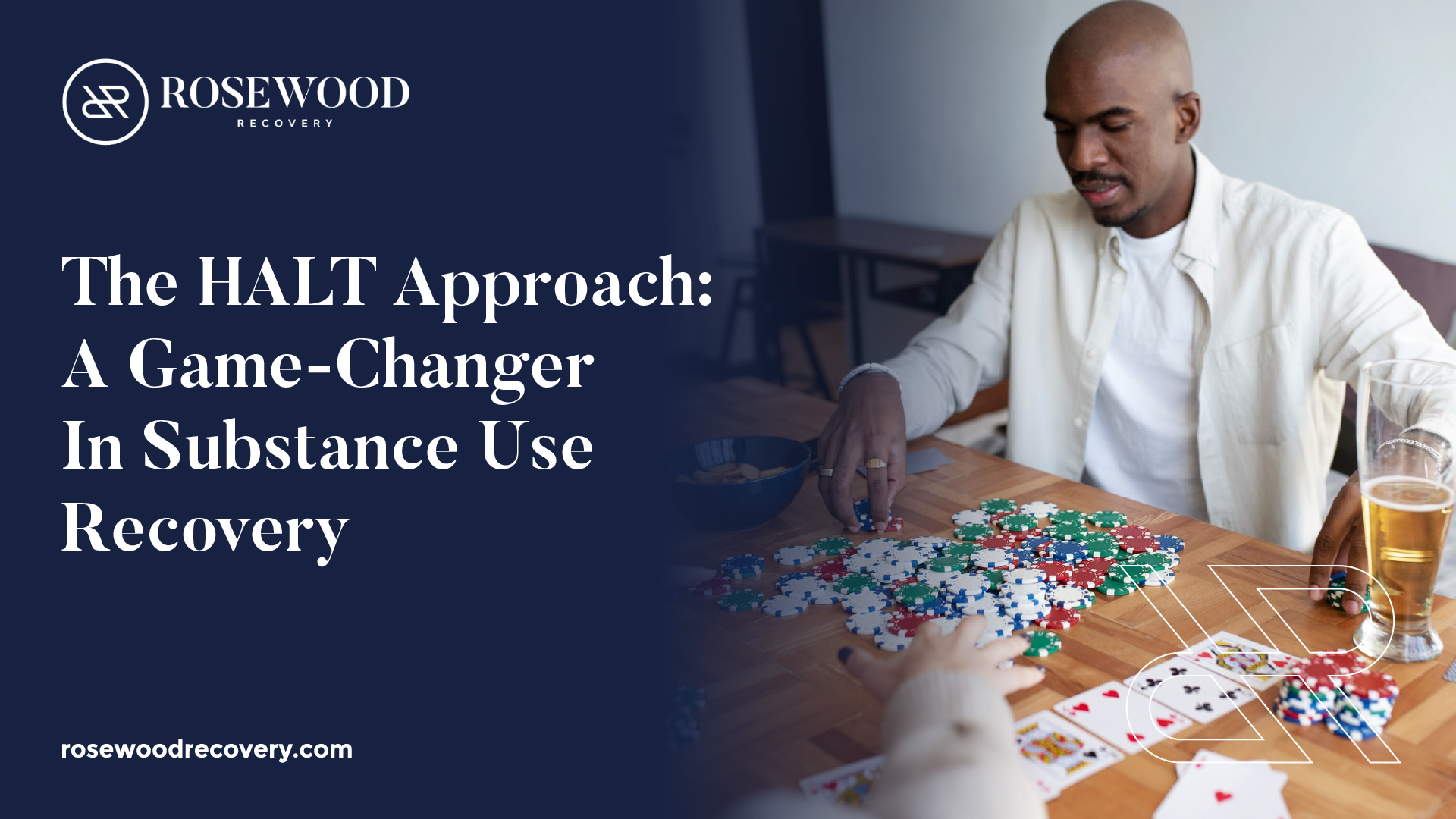
Introduction to HALT
HALT, or Highly Accelerated Life Testing, is a stress testing methodology employed in the industry to enhance product reliability. It involves subjecting prototypes to harsh operating conditions, pushing them beyond their limits to uncover potential weaknesses in design or manufacturing. By accelerating the aging process, HALT testing reveals flaws that might not otherwise manifest during normal usage.
Importance of HALT Testing
HALT testing plays a vital role in the product development process. By identifying weaknesses early on, manufacturers can make necessary design improvements, resulting in a more robust and reliable product [2]. The benefits of HALT testing include:
1. Improved Product Design
HALT testing provides engineers with valuable insights into product weaknesses and flaws. By subjecting prototypes to extreme conditions, they can identify design vulnerabilities and make necessary modifications to enhance the product's performance and durability. This proactive approach helps minimize the possibility of costly warranty services and expensive product recalls after release.
2. Cost Reduction and Time Efficiency
Conducting HALT testing during the early stages of product development enables manufacturers to identify flaws and weaknesses promptly. By addressing these issues early on, design changes can be implemented before production begins, preventing costly modifications later in the process. This leads to cost reduction and improved time efficiency in the overall product development cycle.
3. Reliability Enhancement
By subjecting prototypes to extreme stress levels, HALT testing identifies potential failure points and areas for improvement. The insights gained through this accelerated testing process allow engineers to enhance the reliability of the product. This, in turn, leads to increased customer satisfaction and confidence in the product's performance and longevity.
HALT testing can be applied at various stages of a product's life cycle, including during development, product introduction, and even after a product has been released to the market. By utilizing this methodology throughout the product's lifecycle, manufacturers can continuously audit and improve product reliability.
Understanding the introduction and importance of HALT testing sets the foundation for comprehending the process, benefits, and impact of this testing methodology. It allows manufacturers to build more reliable and robust products, enhancing customer satisfaction and minimizing costly after-sales support.
The Process of HALT Testing
To fully understand the benefits and impact of Highly Accelerated Life Testing (HALT), it's important to delve into the process of HALT testing itself. This section focuses on commencing HALT testing, the difference between HALT and HASS, and the stresses applied during HALT.
Commencing HALT Testing
HALT testing is ideally initiated when prototypes of a product are first available. This early stage of testing allows engineers to identify and address any flaws or weaknesses in the design before it progresses further. By identifying these issues early on, manufacturers can make design changes that are both cost-effective and time-efficient, preventing potentially costly modifications at later stages.
HALT vs. HASS
HALT and Highly Accelerated Stress Screening (HASS) are collectively referred to as Accelerated Stress Testing (AST). While HALT focuses on identifying the operating and destruct limits of a design, HASS is performed on production units to screen for potential defects and weaknesses. HALT and HASS subject products to a series of overstresses, exposing any weak links that may emerge due to accelerated fatigue.
Stresses Applied in HALT
In HALT testing, products are subjected to a combination of stresses to simulate real-world conditions and accelerate the discovery of potential failures. These stresses typically include random six-degree-of-freedom vibration and rapid thermal change rates. By subjecting the product to these combined stresses, HALT testing can help identify weaknesses, design limitations, and potential failure modes that may not surface during traditional testing methods.
By subjecting products to extreme conditions beyond their design specifications, HALT testing pushes the limits of the design to uncover weaknesses. This provides engineers with valuable insights to improve the product's design, increase its robustness, and minimize the possibility of costly warranty services or product recalls after release [2].
Understanding the process of HALT testing is essential for manufacturers seeking to improve product reliability, reduce warranty costs, and enhance customer satisfaction. By commencing HALT testing at an early stage, distinguishing between HALT and HASS, and applying the appropriate stresses, manufacturers can uncover design weaknesses and make necessary improvements to create robust and reliable products.
Benefits of HALT Testing
HALT testing, which stands for Highly Accelerated Life Testing, provides a range of benefits that are instrumental in improving product design, reducing costs, increasing time efficiency, and enhancing reliability.
Product Design Improvement
One of the key advantages of HALT testing is its ability to identify weak points and vulnerabilities in product design early in the development phase. By intentionally inducing stress and subjecting the product to extreme conditions, HALT testing reveals design flaws that may not be apparent under normal operating conditions. This valuable insight allows engineers to make iterative improvements, enhancing the robustness and durability of the product. Addressing these issues during the design stage helps prevent costly warranty services and expensive product recalls after release, ultimately leading to a better product design.
Cost Reduction and Time Efficiency
By using HALT testing, engineers can optimize their designs early on, leading to significant cost reduction and time efficiency throughout the product development process. Identifying and rectifying potential issues at an early stage avoids costly rework later on. Quick iterations and design adjustments enabled by HALT testing significantly shorten the time-to-market for new and improved products, giving companies a competitive edge. This efficient approach helps streamline the product development cycle and ensures that the final product meets or exceeds customer expectations.
Reliability Enhancement
HALT testing plays a crucial role in enhancing the reliability of products. By subjecting the product to extreme stress and accelerated aging, engineers can identify potential issues in the supply chain, vendor shifts, or the overall design. This proactive approach enables them to address and rectify these issues before the product reaches the market, resulting in a more reliable and robust end product [4]. By optimizing designs early on, HALT testing instills confidence in the product's reliability, bolstering trust among consumers and increasing overall customer satisfaction.
HALT testing offers numerous benefits that are invaluable in the product development process. By improving product design, reducing costs, increasing time efficiency, and enhancing reliability, HALT testing empowers engineers to create innovative, high-quality products that meet the evolving needs of the market.
Application of HALT Testing
HALT testing, the acronym for Highly Accelerated Life Testing, can be applied at various stages of a product's lifecycle to ensure its reliability and robustness. Let's explore how HALT testing is utilized during different phases, the test-to-fail technique employed, and the monitoring and equipment used in the process.
Product Lifecycle Stages
HALT testing can be incorporated at different stages of a product's life cycle, providing valuable insights and improvements. It can be employed during product development to identify design weaknesses early on, allowing engineers to make iterative improvements and rectify potential issues before the product reaches the market. Additionally, HALT testing can be conducted during product introduction to uncover any issues caused by new manufacturing processes. Furthermore, it can be used to audit product reliability after a product has been introduced due to changes in components, manufacturing processes, or suppliers.
Test-to-Fail Technique
In HALT testing, the test-to-fail technique is employed, intentionally subjecting the product to extreme stress levels to identify its weak points. By pushing the product beyond its normal operating limits, engineers can uncover design flaws, vulnerabilities, and potential failure modes. This proactive approach allows for early identification and rectification of issues, leading to a more reliable and robust end product.
Monitoring and Equipment Used
During HALT testing, a variety of monitoring techniques and equipment are employed to gather data and assess the product's performance. These can include temperature sensors, vibration sensors, and power analyzers. These instruments help capture and analyze the product's response to the applied stresses, allowing engineers to evaluate its behavior under extreme conditions.
Monitoring and data collection play a crucial role in HALT testing as they provide valuable insights into the product's performance, allowing engineers to identify areas for improvement and make necessary design adjustments. Real-time monitoring helps in capturing any deviations, anomalies, or failure points, enabling engineers to address and rectify issues promptly.
By utilizing HALT testing during the product's life cycle, engineers can optimize their designs, reduce time-to-market for new and improved products, and instill confidence in the product's reliability. This, in turn, leads to increased customer satisfaction, as the products are more robust and trustworthy.
HALT testing provides a proactive and comprehensive approach to product development, allowing engineers to identify and rectify potential issues early on. By intentionally inducing stress and revealing design flaws, HALT testing enables engineers to optimize their designs, shorten the time-to-market, and enhance product reliability, ultimately leading to increased customer satisfaction.
HALT Testing Methodology
In order to effectively conduct Highly Accelerated Life Testing (HALT), a specific methodology is followed, encompassing operational and destruct limits, grms (root mean square acceleration) measurement, and iterative improvements.
Operational and Destruct Limits
HALT involves determining both the Operational Limit and the Destruct Limit of a product [5]. The Operational Limit refers to the stress level at which the product begins to exhibit improper operation but can still return to correct operation. The Destruct Limit, on the other hand, represents the stress level at which the product becomes inoperable and cannot return to correct operation. By determining these limits, engineers gain valuable insights into the product's robustness and its ability to withstand stress.
Grms in HALT Testing
During a HALT procedure, various environmental stresses are applied to the product, including hot/cold temperatures, temperature cycles, random vibration, power margining, and power cycling. These stresses go significantly beyond the expected levels during normal use. To measure the vibration levels, grms (root mean square acceleration) is often used. Grms gives an indication of the overall acceleration levels experienced by the product, helping to identify potential weaknesses and vulnerabilities.
Iterative Improvements through HALT
One of the key benefits of HALT testing is the ability to make iterative improvements to the product design. Engineers can rapidly assess their designs, identify potential issues, and make necessary adjustments early in the development process. This allows for a more efficient and streamlined product development cycle, ultimately resulting in a faster time-to-market for innovative products. By addressing and rectifying issues during HALT testing, engineers can ensure a more reliable and robust end product, instilling confidence in its performance and increasing customer satisfaction.
By following the HALT testing methodology, engineers can push products to their operational and destruct limits, measure grms to assess vibration levels, and make iterative improvements to optimize designs. This approach leads to enhanced product reliability, faster time-to-market, and increased customer satisfaction. HALT testing plays a crucial role in ensuring that products are robust, reliable, and capable of withstanding the stresses they may encounter throughout their lifecycle.
Impact of HALT Testing
Implementing the HALT (Highly Accelerated Life Testing) approach can have several significant impacts on product development and overall success. Let's explore some of the key benefits that HALT testing brings to the table.
Time-to-Market Acceleration
HALT testing plays a crucial role in shortening the time-to-market for new and improved products. By subjecting products to rigorous accelerated testing, engineers can quickly identify weaknesses and areas for improvement. This allows for quick iterations and design adjustments, ensuring that the final product is both reliable and optimized. The ability to identify and address potential issues early in the development cycle significantly speeds up the overall product development process.
Product Robustness and Reliability
One of the primary benefits of HALT testing is its contribution to product reliability. By exposing latent defects and weaknesses under accelerated conditions, engineers can make necessary modifications to the design, materials, or manufacturing processes. This iterative approach leads to a more robust and reliable product [4]. Addressing these weaknesses early on ensures that the end product can withstand real-world conditions, reducing the risk of costly product failures and recalls.
Customer Satisfaction Benefits
HALT testing not only enhances product reliability but also instills confidence in the product's performance. By optimizing designs and making iterative improvements through the testing process, engineers can deliver innovative products that meet or exceed customer expectations. This, in turn, bolsters trust in the brand and increases customer satisfaction. Customers are more likely to be satisfied with a product that has undergone thorough testing to ensure its reliability and performance.
In summary, HALT testing has a significant impact on the product development process. It accelerates time-to-market by allowing for quick iterations and design adjustments, enhances product robustness and reliability, and ultimately leads to increased customer satisfaction. By embracing the HALT approach, companies can optimize their product development strategies and deliver high-quality, reliable products to the market.
References
[2]:
[3]:
[4]:
[5]:
More Articles
Recovery Begins Here
Click below to get in touch and schedule a consult call with our team to begin your journey towards happiness and freedom.
Rosewood Recovery does not discrimate against any person because of the race, color, religious creed, ancestry, age, sex, sexual orientation, gender identity, national origin, handicap or disability or the use of a guide or support animal because of the blindness, deafness or physical handicap.